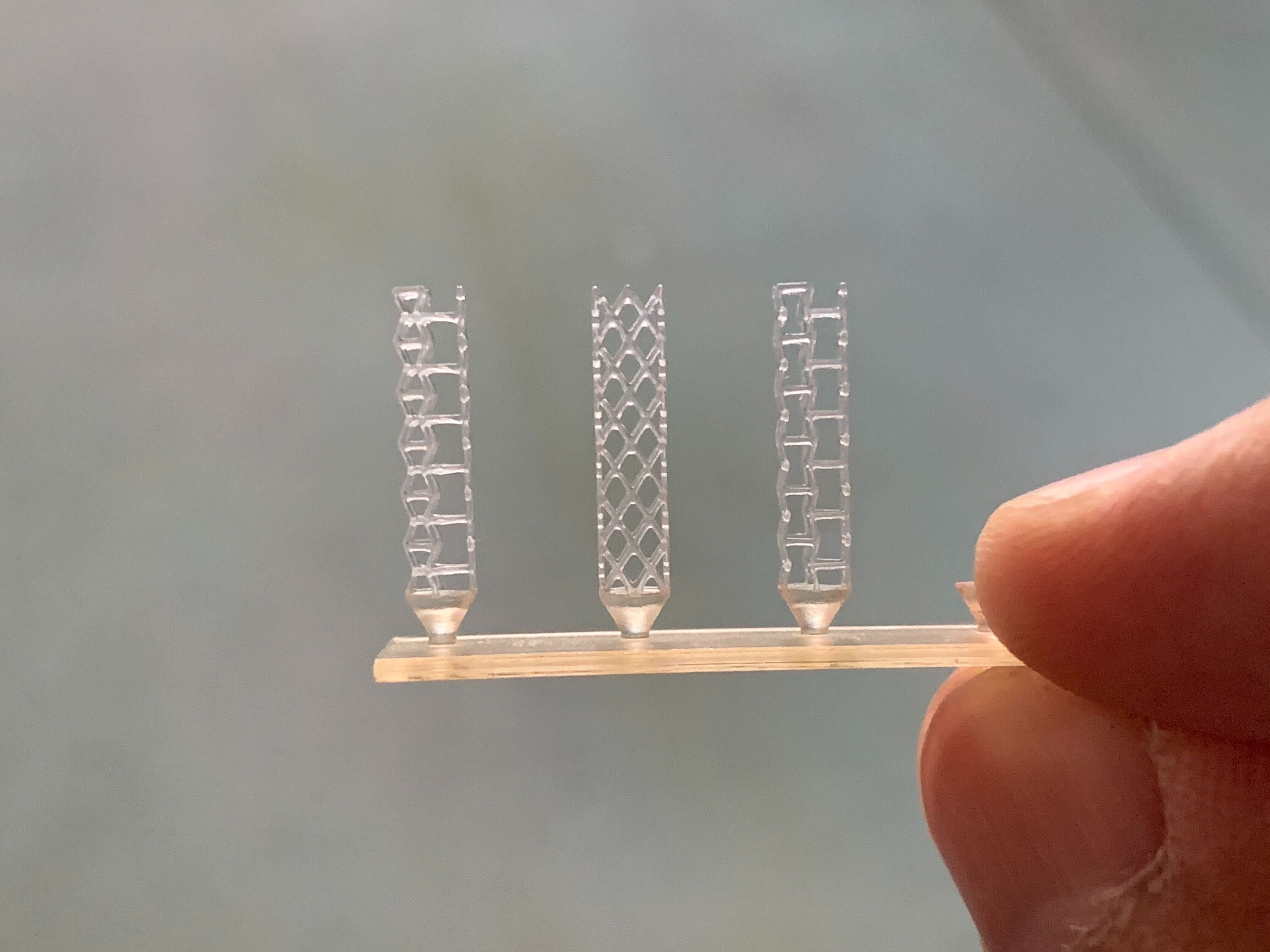
Centre for Engineering Innovation and Research (CEIR)
The Centre for Engineering Innovation and Research (CEIR) is focused on combining advanced scientific techniques, specialist knowledge and critical enquiry to solve engineering problems relevant to the industry, society, healthcare, and the environment. From advanced additive manufacturing to metamaterials, tissue engineering biomaterials, next-generation energy-absorbing devices, and advanced energy storage, the innovations at CEIR are focused on pushing the boundaries of engineering through interdisciplinary enquiry. The centre encompasses multiple research groups focused on in-depth enquiry into various cross-cutting and interdisciplinary thematic areas.
CEIR Impact
For REF 2021 an Impact Case Study was submitted based on our work around additive manufacturing of functional materials. The case study showcased our innovative work with a number of commercial partners across the aeronautical and aerospace sectors.
For information regarding research activities or collaborations, please contact Dr Arun Arjunan (a.arjunan@wlv.ac.uk) who is the Director of the Centre for Engineering Innovation and Research.
Self-funded PhD Projects
To apply for one of the self-funded PhD projects listed below, please complete the PhD Postgraduate research in Engineering course application form by clicking on Apply Now:
PhD Postgraduate research in Engineering - University of Wolverhampton (wlv.ac.uk)
Choose one project listed below and specify the reference number in your application form.
Self-funded Projects PhD Postgraduate research in Engineering
Click here
Reference: 11/MA-24/CEIR
Project details
As climate change is of special concern in the aviation world, highly efficient wing designs are of interest with novel configurations. One promising idea is the highly flexible wing with high aspect ratios. These wings, when composed from composite materials, bring comparably higher aerodynamic efficiencies and eventually need less fuel. Although laminate unidirectional composites are maturely designed and manufactured in the aviation industry, novel composite types like tow-steered are on the edge of research and require further developments. The latter type of composites, when produced by automatic fibre placements, has the opportunity to optimise the paths with different objectives. For this purpose, validated modelling approaches are required. The focus of this research would be the development of such reliable models. The development of the validated model enables the application of novel composite configurations in the structural components of a civil aircraft like the wing and hydrogen tanks for the future hydrogen-powered aviation.
Introduction
For an introduction to the topic and the open areas of research, please refer to the article in the magazine CompositesWorld:
https://www.compositesworld.com/articles/tow-steering-part-2-the-next-generation
There have been papers for related work performed by the University of Michigan as the pioneers of multi-disciplinary optimisations (Brooks et al., 2016; Brooks and Martins, 2018) and further published works in aircraft and wind turbine applications (Barr and Jaworski, 2019; Stodieck et al., 2017).
Research phases
Below, you can see suggestions for the research phases. The focus would be on the development of appropriate models. At each phase, described below, the candidate is expected to publish the outcomes in highly reputed scientific journals.
- Literature review
- Conceptual design for the type of the composite with respect to the needs and the works available in the literature
- Development of a low-fidelity model (beam-type as an example) incorporation the aeroelastic loads and the dynamic response in flutter.
- Development a high-fidelity model capable of TRL 2-3 targeting decarbonizing aviation.
- Development of an optimisation framework and optimise the structure.
- Plan the future steps and opportunities arising from application of the developed predictive and optimisation frameworks.
References
Barr, S.M., Jaworski, J.W., 2019. Optimization of tow-steered composite wind turbine blades for static aeroelastic performance. Renew Energy 139, 859–872. https://doi.org/10.1016/j.renene.2019.02.125
Brooks, T.R., Kennedy, G., Martins, J.R.R.A., 2016. High-fidelity Aerostructural Optimization of a High Aspect Ratio Tow-steered Wing. 57th AIAA/ASCE/AHS/ASC Structures, Structural Dynamics, and Materials Conference. https://doi.org/10.2514/6.2016-1179
Brooks, T.R., Martins, J.R.R.A., 2018. On manufacturing constraints for tow-steered composite design optimization. Compos Struct 204, 548–559. https://doi.org/10.1016/J.COMPSTRUCT.2018.07.100
Stodieck, O., Cooper, J.E., Weaver, P.M., Kealy, P., 2017. Aeroelastic tailoring of a representative wing box using tow-steered composites. AIAA Journal 55, 1425–1439. https://doi.org/10.2514/1.J055364
Supervisory Team: Dr Morteza Abouhamzeh, Lecturer of Aerospace Engineering
For more information: For an informal discussion please email Dr Morteza Abouhamzeh morteza.abouhamzeh@wlv.ac.uk
Reference: 28/TB-24/CEIR
Project details
Increased greenhouse gas (GHG) emissions are the inevitable outcome of a rapidly growing population combined with both increasing industrialization and energy demands across the globe. Currently, over 40 billion tonnes of carbon are released into the atmosphere annually [1], where 34 billon tonnes per year of CO2 is result of fossil fuels [2]. Prior to the onset of the Industrial Revolution in the mid-1700s, the concentration of atmospheric CO2 stood at 280 parts per million (ppm) or lower but the current global average concentration of CO2 in the atmosphere is 421 ppm. Therefore, by 2050, a reduction of 50 percent CO2 emissions, from 1990 levels, is required [3].
Approximately 75% of the world's hydrogen is currently produced from steam methane reforming (SMR) [4], a process that emits a significant amount of CO2 into the atmosphere, resulting in what is known as grey hydrogen. It requires about 1.392 mmbtu of methane to produce 1 mmbtu of hydrogen (in LHV) [5], leading to onsite CO2 emissions of about 9.4 kg/kg H2. SESMR, or steam methane reforming with CO2 capture, offers a solution to this issue by utilizing adsorption technology to capture CO2 and produce blue hydrogen [6]. The effectiveness of both catalysts in the SMR process and sorbents in the absorption unit significantly impacts SESMR [7].
This study focuses on process modelling, cost analysis, and life cycle assessment of using different catalysts and sorbents recommended by experts to capture CO2 and convert grey hydrogen to blue hydrogen. We will screen various catalysis and sorbents and evaluate their effectiveness and efficiency in terms of carbon capture, catalyst stability and activity, and energy consumption in an experimental setup. Experimental data will be used to develop models in Aspen Adsorption and Aspen Plus software, which will be validated against the experimental results. The expected outcomes of the study include three research papers and one review paper.
References
[1] Friedlingstein P, O’sullivan M, Jones MW, Andrew RM, Gregor L, Hauck J, et al. Global Carbon Budget 2022. Earth Syst Sci Data 2022;14:4811–900. https://doi.org/10.5194/ESSD-14-4811-2022.
[2] Carbon Dioxide Emissions From Electricity - World Nuclear Association n.d. https://world-nuclear.org/information-library/energy-and-the-environment/carbon-dioxide-emissions-from-electricity.aspx (accessed January 29, 2024).
[3] Borhani TNG, Akbari V, Afkhamipour M, Hamid MKA, Manan ZA. Comparison of equilibrium and non-equilibrium models of a tray column for post-combustion CO<inf>2</inf>capture using DEA-promoted potassium carbonate solution. Chem Eng Sci 2015. https://doi.org/10.1016/j.ces.2014.09.017.
[4] Sun P, Elgowainy A. Updates of Hydrogen Production from SMR Process in GREET ® 2019. 2019.
[5] Hydrogen Fact Sheet: Production of Low-Carbon Hydrogen - Center on Global Energy Policy at Columbia University SIPA | CGEP n.d. https://www.energypolicy.columbia.edu/publications/hydrogen-fact-sheet-production-of-low-carbon-hydrogen/ (accessed March 27, 2024).
[6] Capa A, Yan Y, Rubiera F, Pevida C, Gil MV, Clough PT. Process Simulations of High-Purity and Renewable Clean H2 Production by Sorption Enhanced Steam Reforming of Biogas. ACS Sustain Chem Eng 2023;11:4759–75. https://doi.org/10.1021/ACSSUSCHEMENG.2C07316/ASSET/IMAGES/LARGE/SC2C07316_0009.JPEG.
[7] Nkulikiyinka P, Wagland ST, Manovic V, Clough PT. Prediction of Combined Sorbent and Catalyst Materials for SE-SMR, Using QSPR and Multitask Learning. Ind Eng Chem Res 2022;61:9218–33. https://doi.org/10.1021/ACS.IECR.2C00971/ASSET/IMAGES/LARGE/IE2C00971_0017.JPEG.
Supervisory Team
Dr Tohid Borhani, Senior Lecturer in Chemical Engineering and Dr Abul Arafat, Lecturer in Materials Engineering
For more information: For an informal discussion please email Dr Tohid Borhani t.borhani@wlv.ac.uk
Reference: 23/AE-24/CEIR
About the Project
In this project, we will couple emulsion templating, a versatile method used to create porous polymers, with lithographic 3D printing approaches to create a range of complex architecture scaffolds for tissue engineering.
In the emulsion-templating method, a high internal phase emulsion (HIPE) is created in which the continuous, or non-droplet, phase contains one or more polymerisable monomers. Polymerisation then results in a polymeric material, known as a polyHIPE, of dimensions and shape determined by the vessel or mould in which the HIPE was contained. Recent work has created biodegradable and biocompatible materials by photochemical thiol-ene polymerisation employing commercially available multifunctional thiols and acrylates. In this project, microstereolithography (μSL) / Digital Light Processing (DLP), which uses a finely focussed projected light source to selectively solidify a photocurable polymer resin, will be used to create porous scaffolds with well-defined and complex geometries. Successive images representing cross-sections of a 3D computer-aided design (CAD) file are shone onto a thin film of polymer precursor in order for it to solidify. An accurate motion stage raises the polymer film by a preselected amount and a further layer of polymer resin is solidified. In this way, geometrically complex 3D objects can be manufactured in a layer-by-layer fashion without the need for moulds or machining.
The project will have 3 phases:
- Development of novel curable resins for creating porous 3D scaffolds. Commercially available multifunctional monomers for thiol-ene polymerisation, including acrylates, vinyl ethers, allyl compounds and thiols will be trialled in this regard.
- Creation of 3D printed scaffold test-pieces, including tubes and blocks with internal chambers, channel arrays and interconnected channel networks.
- In partnership with internal and external biomedical researchers, investigation of the use of these scaffolds for the 3D culture of a variety of cell types, including epithelial cells and endometrial stem cells.
This project is part of ongoing research, so is suitable for either Engineering or Chemistry PhD students as the direction of work can be adapted and shifted from one aspect to another with support from the team.
Relevant recent references
- C. J. Atkins, et al., “Branched macromonomers from catalytic chain transfer polymerisation (CCTP) as precursors for emulsion-templated porous polymers”, Polymer Chemistry 2020, 11, 3841-3848.
- A. M. Eissa, et al., “Enhanced Differentiation Potential of Primary Human Endometrial Cells Cultured on 3D Scaffolds”, Biomacromolecules 2018, 19, 8, 3343-3350.
- C. Chen, A. M. Eissa, et al., "Emulsion-templated porous polymers prepared by thiol-ene and thiol-yne photopolymerisation using multifunctional acrylate and non-acrylate monomers", Polymer 2017, 126, 395–401.
- A. M. Eissa, et al., “Reversible surface functionalisation of emulsion-templated porous polymers using dithiophenol maleimide functional macromolecules”, Chemical Communication 2017, 53, 9789 - 9792.
- D.W. Johnson, et al., “Macrostructuring of Emulsion-templated Porous Polymers by 3D Laser Patterning”, Adv. Mater. 2013, 25, 3178-3181.
Supervisory Team
Dr Ahmed M. Eissa (Senior Lecturer) and Professor Arun Arjunan (Chair)
For more information: For an informal discussion please email Dr Ahmed Eissa A.M.Eissa@wlv.ac.uk
Reference: 30/AA-24/CEIR
Project details
Recently, there has been a rapid increase in the number of bone deformities due to traffic accidents, sports injuries, and various illnesses. Bone defects can arise as a result of fracture, infection, and surgical removal of bones. As a result, worldwide, more than 2 million patients receive bone grafts each year. The clinical and financial burden related to bone abnormalities has logically increased with time, as seen by the 33.4% increase in new bone fracture occurrences over the last three decades. Bone abnormalities are more common than expected, which leads to both chronic pain and more importantly, a loss of bone function, which dramatically lowers patients' quality of life. An appropriate bone scaffold with certain qualities is required to solve this problem. Among them, (i) excellent biological qualities like biocompatibility, bioactivity, and biodegradability (to allow for new bone formation); (ii) interconnected pores with varying pore size; (iii) osteoconductive properties; and (iv) shape and size tailored to the defect size. Following the clarification of the need, several materials such as metals, alloys and polymers that address these features have been developed via additive manufacturing and investigated for their potential in the healing of bone defects. However, metals and polymers are minimally resorbable, biocompatible, and cause little toxic reactions or foreign body reactions. Additive manufacturing of phosphate glass can be utilised as an alternative material of the aforementioned issues. A high-precision, patient-specific geometry and precise control of the complicated porosity structure are only a couple of the advantages of using AM in the manufacture of glass tissue engineering scaffolds. Phosphate glass is an excellent biomaterial due to its biodegradability, high calcium content, biocompatibility, and controllable rate of degradation. The advantages of phosphate glasses over other glasses are their lower melting temperatures, high thermal expansion coefficient and ability to accommodate high concentrations of metal oxides. However, little attention has been made on additive manufacturing of glasses to shape it into necessary geometry due to its amorphous structure, lack of ductility and high melting temperature which makes it challenging. To overcome these, titanium will be incorporated in the phosphate glass as titanium will induce bioactivity and improve mechanical stability. Tetravalent titanium in phosphate glass is found to ionically cross-link the phosphate units, disrupting the glass network and resulting in a decrease in hydrolyzable P-O-P bonds, which is essential for bioactivity. As a result, the surrounding media's ability to become acidic is hindered, which leads to the precipitation of bioactive hydroxyapatite. As such, titanium phosphate-glasses in the system 40P2O5–25Na2O–(35-x)CaO–xTiO2 (0≤x≤10) are considered in this study which will be prepared via melt quenching and solid spherical glass particles (63-80 µm) will be produced via a flame spheroidisation process. Among different additive manufacturing techniques, this research will focus on the laser powder bed fusion (LPBF) process of titanium phosphate glasses and optimisation of the process parameters such as laser power, layer thickness and scanning speed will be carried out which will enable the formation of complex geometry, necessary for bone regeneration implants.
Supervisory Team
Dr Abul Arafat, Lecturer in Materials Engineering
For more information: For an informal discussion please email Dr Abul Arafat a.arafat@wlv.ac.uk
Reference: 37/MA-24/CEIR
Project details
Aerodynamic force acting on turbine blades is affected by the turbulence, wind velocity and attack direction. The unsteady wind velocity and its constantly varying direction cause the structure vibration and dynamic stall. This is particularly true for the next generation of large composite blade structures of offshore wind turbines. The use of larger turbine blades would result in significant improvements in efficiency and reductions in wind energy cost, but large lightweight blades are more susceptible to aero-elastic influences. Therefore, accurate prediction of the aerodynamic loading and the structural response of turbine blades is of vital importance to determine the electricity output, the turbine blade design and materials used. This is especially true for large turbines due to the lack of available experimental data on large turbine blades.
There are three major weak points in the currently available fluid-structure coupled simulation frameworks applied to wind turbines:
- Lack of accuracy in numerical simulation of flow over turbine blades using the Unsteady Reynolds Averaged Navier-Stokes (URANS) which benefits from low computational cost.
- Extremely high computational cost of using high fidelity approaches Large Eddy Simulation (LES) and Direct Numerical Simulation (DNS) making them impractical choice.
- Two standalone codes (one for flow simulation and one for structural analysis) are used and data need to be transferred at every time-step between two codes, which is very inefficient and also may lead to inaccurate results.
Aim and objectives:
Aim: Development an integrated flow-structure solver applicable to simulate very large-scale wind turbines addressing the above weaknesses
OBJ1. Develop a numerical technique coupling a flow solver, a turbine model and a structure solver.
OBJ2. Validate the developed numerical method against available experimental data.
OBJ3. Apply the developed numerical method to simulate very large wind turbines.
Methodology: A hybrid method coupling LES and actuator line modelling (ALM) (Ahmad & Yang 2020) will be employed in the proposed project to provide a very accurate prediction of flow field and aerodynamic loading on turbine blades. Turbine blades will be modelled by the ALM technique so that this hybrid approach reduces the computational cost significantly and gets rid of grid structure complexity around turbine blades compared with a pure LES approach. Our flow simulation code based on this hybrid approach has been developed and used to simulate wind/tidal turbine flows accurately (Ahmadi & Yang 2021, 2022). The structural analysis will be carried out using the Geometrically Exact Beam Theory (GEBT), which is a nonlinear aero-elastic model suitable for the investigation of large, flexible rotor blades (Dose et al. 2018). The structural analysis model will be implemented in our flow simulation code under the OpenFOAM framework without the explicit data transfer between two standalone codes, greatly improving the fluid-structure coupled simulation efficiency.
Supervisory Team
Dr Mohammad Ahmadi, Lecturer in Mechanical Engineering
For more information: For an informal discussion please email Dr Mohammad Ahmadi Ahmadi.M@wlv.ac.uk
Reference: 45/AA-24/CEIR
Project details
Additive manufacturing (AM) has emerged as a revolutionary technology in the manufacturing industry, offering unprecedented design flexibility and manufacturing freedom. Laser beam forming (LBF) technology, a subset of Laser Powder Bed Fusion (L-PBF), holds promise for the production of complex components, especially those made from refractory metals and their alloys. Refractory metals, characterised by their high melting points and excellent mechanical properties, are widely used in aerospace, automotive, and medical industries for their ability to withstand extreme conditions. However, the successful AM of refractory metal alloys poses significant challenges due to their high reactivity, complex thermo-mechanical properties, and susceptibility to defects. Thus, optimising process parameters becomes crucial to unlock the full potential of laser beam forming technology for refractory metal alloy manufacturing.
Rationale/Problem
Despite the growing interest in using laser beam forming for refractory metal alloy AM, there is a lack of comprehensive understanding regarding the optimal process parameters required to achieve high-quality components. Existing studies often focus on a limited range of parameters or overlook the intricate interactions between various factors, leading to suboptimal outcomes. Consequently, there is a pressing need to systematically investigate and optimise the process parameters involved in LBF-based AM of novel refractory metal alloys to enhance part quality, mechanical properties, and production efficiency.
Methodologies
This research project will employ a multifaceted approach to address the optimisation of process parameters for AM of novel refractory metal alloys using LBF technology. Initially, a comprehensive review of the literature will be conducted to identify the key process parameters, material characteristics, and challenges associated with refractory metal alloy AM. Subsequently, experimental investigations will be carried out to systematically explore the effects of various process parameters, including, beam shape, laser power, scan speed, layer thickness, powder characteristics, and inert gas atmosphere, on the quality and properties of fabricated components. Design of experiments (DOE) methodologies coupled with statistical analysis and artificial intelligence (AI) algorithms will be employed to systematically study the parameter interactions and optimise the process conditions. Advanced characterization techniques such as X-ray computed tomography (XCT), X-ray diffraction (XRD), and mechanical, thermal and acoustic testing will be utilized to evaluate the microstructural evolution, phase transformations, and performance of the manufactured parts.
Expected outputs
- A comprehensive understanding of the effects of process parameters on the quality, microstructure, and properties of AM-fabricated refractory metal alloy components.
- Optimisation guidelines for selecting optimal process parameters to enhance part quality, mechanical properties, and production efficiency in LBF-based AM of novel refractory metal alloys.
- Novel insights into the microstructural evolution and phase transformations occurring during the AM process, enabling informed process design and control strategies.
- Publication of research findings in peer-reviewed journals and presentation at relevant conferences to disseminate knowledge and contribute to the advancement of additive manufacturing technologies.
- Contribute new insights, methodologies, and guidelines for the additive manufacturing of refractory metal alloys using laser beam forming technology. Provide recommendations for optimising process parameters to enhance the efficiency, quality, and reliability of AM processes in industrial applications.
- Explore potential applications in aerospace, automotive, and medical industries, leading to improved performance, reduced lead times, and cost savings in the production of refractory metal alloy components.
Supervisory Team
Prof Arun Arjunan, Director of the Centre of Engineering Innovation and Research (CEIR)
Dr John Robinson, Additive Manufacturing Research Commercialisation Manager
For more information: For an informal discussion please email Prof Arun Arjunan A.Arjunan@wlv.ac.uk or Dr John Robinson J.Robinson12@wlv.ac.uk
Reference: 46/AA-24/CEIR
Project detail
Additive manufacturing (AM), commonly known as 3D printing, has revolutionised manufacturing processes by enabling the production of complex geometries with unprecedented precision and efficiency. Metamaterials, engineered materials with unique properties not found in nature, offer tremendous potential for applications ranging from aerospace to biomedical devices. However, traditional manufacturing methods often limit the design possibilities and performance of metamaterials due to their complex structures. Laser beam forming technology, a subset of Laser Powder Bed Fusion (L-PBF), utilises high-powered lasers to selectively melt and fuse metallic powders layer by layer, allowing for the creation of intricate structures. By leveraging this technology, we can overcome the limitations of conventional manufacturing for the creation of process-informed metallic metamaterials.
Rationale/Problem
The conventional manufacturing processes cannot fabricate process-informed metamaterials with intricate architectures that are essential for achieving targeted porosity, stiffness and strength. Moreover, existing metamaterial fabrication techniques often involve complex and costly processes, hindering their widespread adoption and personalisation. This project aims to address these challenges by developing a novel approach that combines the versatility of the beam forming with the design freedom offered by metamaterials. By using laser beam forming technology, we can precisely control the deposition of material, allowing for the creation of customised metamaterial structures tailored to specific applications.
Methodologies
Identify suitable metallic powders with properties conducive to metamaterial applications. Characterise their mechanical, thermal, and electromagnetic properties to ensure compatibility with the desired functionalities. Utilise computational tools such as finite element analysis (FEA) and topology optimisation algorithms to design metamaterial architectures tailored to the targeted properties and performance metrics. Develop optimised laser beam forming parameters, including laser power, scanning speed, and powder feed rate, to achieve precise control over the fabrication process and ensure the integrity of the metamaterial structures. Evaluate the mechanical, acoustic, and electromagnetic properties of the fabricated metamaterials through experimental testing and validation. Iterate the design and fabrication process based on the performance feedback to further enhance the material properties.
Expected outputs
- Fabrication of intricate metamaterial architectures with tailored stiffness and strength properties, surpassing the limitations of conventional manufacturing techniques.
- Experimental validation of the designed metamaterials, demonstrating their superior performance compared to existing materials for specific applications.
- Development of guidelines and best practices for the additive manufacturing of process-informed metamaterials using laser beam forming technology, facilitating the adoption of this approach in various industries.
- Publication of research findings in peer-reviewed journals and presentation at conferences to contribute to the advancement of additive manufacturing and metamaterial research.
Supervisory Team
Prof Arun Arjunan, Director of the Centre of Engineering Innovation and Research (CEIR)
Dr John Robinson, Additive Manufacturing Research Commercialisation Manager
For more information: For an informal discussion please email Prof Arun Arjunan A.Arjunan@wlv.ac.uk or Dr John Robinson J.Robinson12@wlv.ac.uk
Reference: 47/AA-24/CEIR
Project detail
The challenges posed by thermal transfer and heat dissipation are well-documented across diverse industries. In recent years, with the advent of electric vehicles (EVs), renewable energy systems, high-power LEDs, and quantum computing, the need for effective thermal management has become even more pronounced. The demand for efficient heat dissipation solutions stems from the increasing power densities and miniaturisation trends in electronic devices and systems. Traditional thermal management approaches, such as heat sinks and heat exchangers, have been extensively studied and utilised, but they face limitations in meeting the evolving requirements of modern applications. Our research has highlighted the importance of developing advanced materials and manufacturing processes to address localised high heat fluxes and non-uniform heat dissipation challenges.
Rationale/Problem
The rationale for exploring hybrid subtractive and additive manufacturing methodologies lies in addressing the inherent limitations of both approaches. Subtractive manufacturing processes, including CNC machining, are known for their precision but often result in significant material wastage, as highlighted in various studies on sustainable manufacturing practices. On the other hand, additive manufacturing techniques, such as Laser Powder Bed Fusion (L-PBF), offer the potential to reduce material waste and enable the fabrication of complex geometries. However, challenges remain in processing materials like copper efficiently and cost-effectively using AM methods, as reported in previous research. Therefore, there is a compelling need to explore novel approaches that leverage the strengths of both subtractive and additive manufacturing to achieve greener and more sustainable fabrication processes.
Methodologies
Building on the wider literature on manufacturing processes and materials science, the proposed methodology involves a comprehensive assessment of hybrid manufacturing techniques for thermal management components. Drawing from studies on advanced manufacturing technologies, such as hybrid machining and additive/subtractive integration, the project aims to develop innovative solutions that minimize material wastage while maintaining high precision and cost-effectiveness. Leveraging the expertise of interdisciplinary research teams and state-of-the-art facilities, the project will explore the feasibility of integrating laser beam shaping and oxygen control technologies into next-generation L-PBF systems. Insights from recent advancements in laser processing and metallurgy will inform the development of optimised parameters for manufacturing enhanced copper components with superior thermal properties.
Expected outputs
- Optimisation guidelines for integrating subtractive and additive manufacturing processes to minimize material wastage while maintaining precision and cost-effectiveness.
- Insights into process parameters and design considerations for enhancing thermal performance and manufacturability of components including experimental validation of the feasibility and efficacy of the proposed hybrid manufacturing approach.
- Contribution to sustainable manufacturing practices through the reduction of material waste and energy consumption.
- Advancements in the fabrication of thermal management components with superior heat dissipation properties.
- Dissemination of findings through peer-reviewed publications in relevant academic journals and presentations at conferences. Contribution to the broader scientific community by providing insights and methodologies applicable to diverse industrial sectors.
Supervisory Team
Prof Arun Arjunan, Director of the Centre of Engineering Innovation and Research (CEIR)
Dr John Robinson, Additive Manufacturing Research Commercialisation Manager
For more information: For an informal discussion please email Prof Arun Arjunan A.Arjunan@wlv.ac.uk or Dr John Robinson J.Robinson12@wlv.ac.uk
Reference: 48/AA-JR/24
Project detail
Copper (Cu) holds a pivotal role in various applications owing to its excellent thermal and electrical properties. With the global shift towards net-zero initiatives, the demand for copper is poised to escalate, particularly in renewable energy and electrified transportation sectors. Additive Manufacturing (AM) presents a promising avenue for fabricating custom copper components, offering opportunities to enhance efficiency through optimised materials, bespoke geometries, and integrated cooling strategies. However, Laser Powder Bed Fusion (L-PBF), the leading AM technology for metals, faces significant challenges when processing highly reflective and conductive metals like copper. These challenges stem from inadequate energy absorption by conventional infrared laser wavelengths (1060–1090 nm), resulting in high laser reflectivity. Additionally, copper’s propensity for oxidation further complicates the printing process by leading to the formation of oxide layers on powder feedstock. Addressing these challenges requires a comprehensive understanding of the material-laser interaction to maximise material absorptivity while minimising laser reflectivity.
Rationale/Problem
Current approaches to mitigating the challenges of L-PBF processing of copper include alloying, alternative wavelength lasers, and higher power lasers. However, these approaches have limitations, necessitating innovative solutions for successful fabrication of copper components. Emerging advancements in L-PBF technology, such as next-generation laser beam shaping and process chamber gas composition control, offer promising avenues for overcoming these challenges. By harnessing these advancements, it becomes possible to achieve precise control over laser energy and oxygen levels during printing, thereby enhancing process reliability and component quality. This project seeks to capitalise on recent investments in beam shaping technology and leverage the expertise of the Centre for Engineering Innovation and Research in L-PBF material and process development to explore the feasibility of integrating laser beam shaping and gas composition control for enhanced copper component manufacturing.
Methodologies
The research will involve conducting experiments on a next-generation L-PBF machine equipped with advanced laser beam shaping and process chamber gas composition control capabilities. Through a combination of experimental investigations and computational modelling, the project will evaluate the effectiveness of different gas compositions and laser beam shaping techniques in improving material absorptivity and minimizing laser reflectivity during copper 3D printing. Material characterisation techniques, including microscopy and spectroscopy, will be employed to analyse the microstructural and chemical properties of printed components. Additionally, thermal analysis methods will be utilised to assess the thermal performance of printed copper components. The interdisciplinary nature of the project will facilitate collaboration with experts in material science, laser technology, and additive manufacturing.
Expected outputs
- Development of optimised laser powder bed fusion gas process compositions for enhanced copper 3D printing.
- Evaluation of novel laser beam shaping techniques for improving material absorptivity and minimizing laser reflectivity during copper printing including identification of the material-laser interaction mechanisms governing the successful L-PBF processing of copper.
- Experimental validation of the feasibility and efficacy of integrating laser beam shaping and gas composition control technologies for copper component manufacturing.
- Dissemination of research findings through peer-reviewed publications and presentations at conferences.
- Enhancement of research infrastructure and capabilities in the field of additive manufacturing at the Elite Centre for Manufacturing Skills and Telford Innovation Campus facilities.
Supervisory Team
Prof Arun Arjunan, Director of the Centre of Engineering Innovation and Research (CEIR)
Dr John Robinson, Additive Manufacturing Research Commercialisation Manager
For more information: For an informal discussion please email Prof Arun Arjunan A.Arjunan@wlv.ac.uk or Dr John Robinson J.Robinson12@wlv.ac.uk
Reference: 49/AA-24/CEIR
Project details
Originally developed at NASA’s Glenn Research Center, GRCop alloys represent a class of copper-based alloys tailored for high-temperature aerospace and space applications. Comprising copper (Cu), chromium (Cr), and niobium (Nb), these alloys exhibit exceptional thermal conductivity, creep resistance, low-cycle fatigue life, and elevated temperature strength. They are extensively utilised in the manufacture of critical components such as rocket engine combustion chambers, liners, and fuel injector face plates. With the evolution of additive manufacturing (AM) technologies, particularly Laser Powder Bed Fusion (L-PBF), there has been a paradigm shift in the fabrication of rocket engine components. L-PBF offers unparalleled design freedom and manufacturing potential, enabling the production of complex geometries that surpass the performance of conventionally manufactured components. However, the integration of next-generation laser beam shaping and process chamber gas composition control in emerging L-PBF machines presents new opportunities for advancing the additive manufacturing of GRCop alloys.
Rationale/Problem
Despite the success of L-PBF in manufacturing aerospace components, there remain challenges in optimising the process for GRCop alloys. Achieving precise control over laser energy and process gas composition is critical for ensuring the quality and integrity of printed components. Traditional L-PBF processes may not fully exploit the unique properties of GRCop alloys, leading to suboptimal mechanical properties and microstructural characteristics. By leveraging advancements in laser beam shaping and gas composition control, this project seeks to address these challenges and unlock the full potential of GRCop alloys in additive manufacturing applications.
Methodologies
The research will entail experimental investigations conducted on a next-generation L-PBF machine equipped with advanced laser beam shaping capabilities and process chamber gas composition control. Through systematic experimentation and computational modelling, the project will evaluate various gas compositions and laser beam shaping techniques to optimise the additive manufacturing process for GRCop alloys. Material characterisation techniques, including microscopy, spectroscopy, and mechanical testing, will be employed to assess the microstructural evolution and mechanical properties of printed components. Furthermore, thermal analysis methods will be utilised to evaluate the thermal conductivity and heat dissipation capabilities of the manufactured GRCop alloy components. The interdisciplinary nature of the project will facilitate collaboration with experts in materials science, aerospace engineering, and additive manufacturing.
Expected outputs
- Development of optimised laser powder bed fusion gas process compositions for enhanced additive manufacturing of GRCop copper alloys.
- Evaluation of novel laser beam shaping techniques for improving build quality and mechanical properties of printed GRCop alloy components including identification of microstructural evolution and thermal properties of additive manufactured GRCop alloys.
- Experimental validation of the feasibility and efficacy of integrating laser beam shaping and gas composition control technologies for GRCop alloy additive manufacturing.
- Dissemination of research findings through peer-reviewed publications and presentations at international conferences.
- Establishment of collaborations with aerospace industry partners for technology transfer and application in real-world aerospace components.
- Enhancement of research infrastructure and capabilities in the field of additive manufacturing at the Elite Centre for Manufacturing Skills and Telford Innovation Campus facilities.
Supervisory Team
Prof Arun Arjunan, Director of the Centre of Engineering Innovation and Research (CEIR)
Dr John Robinson, Additive Manufacturing Research Commercialisation Manager
For more information: For an informal discussion please email Prof Arun Arjunan A.Arjunan@wlv.ac.uk or Dr John Robinson J.Robinson12@wlv.ac.uk
Reference: 55/AA-24/CEIR
Project details
Extreme weather events, i.e. extensive droughts and extreme floodings, are being a regular occurrence in several countries globally due to climate change. In the UK, several regions declare drought and water usage regulations on an increasing basis. Therefore, the demand for a cheap, scalable solution to replenish drinking water stocks is increasing.
Triply periodic minimal surface structures (TPMS) are a potential solution due to their unique and complex geometries, based on a base unit cell, that render them with three unique advantages: enhanced surface area, enhanced strength, great scalability. As such, they have attracted considerable scientific and industrial attention recently in several areas including fluid transport to mixing to heat exchangers. In this project, we aim to develop a TPMS cell that will need the least amount of energy input, effectively passive, to collect large amounts of water with the largest possible surface area.
We will combine generative design and topology optimisation principles to develop optimal unit cells for atmospheric water harvester concepts. Benchtop concepts will be 3D printed at our UK Centre of Excellence for Additive Manufacturing. Rigorous testing of mechanical properties, such as strength and longevity, together with controlled fog harvesting experiments will be conducted in our multiscale thermofluids lab.
The successful candidate is expected to train in metal 3D printing using our state-of-the-art AMCM M 290-1 FLX and will be provided with opportunities for networking and showcasing their work. The expected outcomes will be shared in national and international conferences. The candidate will be encouraged to engage with our industrial partners for potential commercialisation.
Supervisory Team
Dr Alex Askounis and Mr Aaron Vance
For more information: For an informal discussion please email Dr Alex Askounis a.askounis@wlv.ac.uk